Aluminum Armor Plate
Chalco armor plate has undergone four generations of research and development, and its representative products are the 5083, 5456, 7039, 2519, 2139 armor plate, and the latest high-tech five-layer, seven-layer, nine-layer composite aluminum armor plate, foam armor plate, honeycomb armor plate and other aluminum composite materials
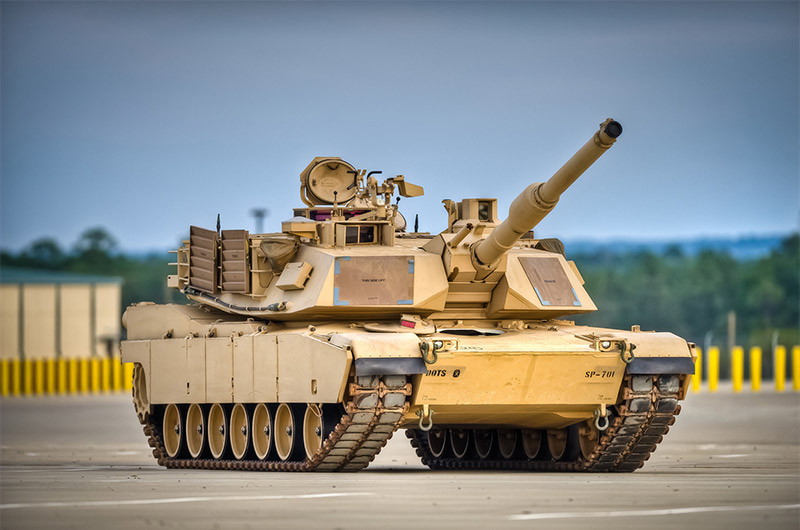
Chalco armor plates have strict quality control and meet standards such as MIL-DTL-32341, MIL-DTL-45225, MIL-DTL-46027, MIL-DTL-46083E, MIL-DTL-32375B, GJB 9614-2019, and GJB 1540-2021. Chalco can provide multiple quality inspections if needed.
Chalco's latest composite armor plate product
Aluminum alloy layered composite armor plate can also be referred to as a "sandwich structure" plate. It is composed of aluminum alloys with higher strength and aluminum alloys with lower strength but better toughness and weldability. The hard layer panel has bulletproof ability, the resilient layer back plate can prevent debris from peeling off, and the separation of the interface between the panel and interlayer can absorb energy in layers. The overall penetration resistance is higher than that of homogeneous armor, and the explosion-proof performance is better.
-
Three-layer composite armor plate
Alloy: 7039 7005 7039
The panel can also be replaced with 5083.
-
Five-layer composite armor plate
Alloy: 7072 7A52 7072 7A62 7072
Thickness(mm): 18, 20, 21, 25, 30 -
Sever-layer composite armor plate
Alloy: 7072 7A52 7072 7A52 7072 7A62 7072
Thickness(mm): 25
Size: 1500×5000 -
Nine-layer composite armor plate
Alloy: 7072 7A52 7072 7A52 7072 7A62 7072 7A62 7072
Thickness(mm): 35, 40
Size: 1500×5000 -
Foam aluminum armor plate
Reduce weight, enhance explosion and impact resistance, and provide sound insulation.
-
Honeycomb aluminum armor plate
More commonly used on the body and roof of light armored vehicles, as well as on ship armor.
Chalco first generation armor plate products
Early armored vehicles were mainly made of steel. With the increasing demand for protective capabilities of armored vehicles in modern warfare, ideal armor materials also need characteristics such as lightweight, impact resistance, high mobility, and corrosion resistance. As the first generation of lightweight armor plates, aluminum alloy plates such as 5083, 5456 were developed and applied under this demand.
-
5083 armor aluminum plate
It can provide good protection against the threat of shrapnel, explosion, and impact.
-
5456 armor aluminum plate
Commonly used in bulletproof vehicles, warships, and military diving equipment.
-
5046 armor aluminum plate
High strength and good weldability, suitable for military armored vehicles and military fighter jets.
-
5059 armor aluminum plate
Relatively high strength and hardness, good corrosion resistance and processability.
-
2024 armor aluminum plate
Good fatigue strength and hardness provide good defense for armored vehicles.
-
6061 armor aluminium plate
Used for ground vehicle armor and industrial machinery armor.
Chalco second generation armor plate products
Most of the first generation aluminum alloy armor plates cannot be strengthened by heat treatment and have poor resistance to direct impact from small caliber projectiles, making it difficult to meet the protection requirements. Chalco second-generation armor plate alloys such as 7039, 7056, 7020, 7017 have made up for these deficiencies and are used to resist high-speed shrapnel, warheads, explosive impacts, and other threats.
-
7039 T64 armor aluminum plate
Armor plates can be manufactured through rolling, forging, extrusion, and other methods.
-
7056 armor aluminum plate
High strength;
Higher impact resistance. -
7020 armor aluminum plate
Moderate strength;
Corrosion resistance;
Weldable aluminum alloy. -
7017 armor aluminum plate
High strength;
Weldable aluminum alloy. -
7018 armor aluminum plate
Can be welded with a thickness of over 50 mm.
-
7A52 armor aluminum plate
High strength;
High hardness;
Excellent elastic modulus. -
7B52 armor aluminum plate
High strength and hardness;
Excellent corrosion resistance. -
7085 armor aluminum plate
High tensile strength;
Excellent corrosion resistance;
High temperature stability. -
7075 armor aluminum plate
Very high tensile strength;
Excellent hardness;
Relatively light.
Chalco third generation armor plate products
To address the ballistic and stress corrosion resistance of aluminum alloys, Chalco third-generation armor plate alloys such as 2519, 2139, 2195 have been introduced, which have higher mechanical properties, ballistic resistance, weldability, and stress corrosion resistance.
-
2519/2519A T87 armor aluminum plate
Higher ballistic performance than 7039;
Better stress corrosion resistance than 5083. -
2139 T8 armor aluminum plate
High tensile strength;
Resistance to elasticity;
High thermal stability. -
2195 T8 P4 armor aluminum plate
Increased strength and hardness;
Good welding performance.
The importance of replacing steel with aluminum in armor plate
- Aluminum has low density and good mechanical properties, which can reduce the weight of armored vehicles and increase driving speed while improving structural stiffness;
- Aluminum has high strength and toughness, with comprehensive performance of anti-penetration and anti-fragmentation;
- Aluminum has better processing performance and is suitable for mass production;
- Aluminum has stronger welding performance, which better adapts to the manufacturing of different models of armored vehicles;
- Aluminum has stronger thermal nuclear resistance, which can effectively protect personnel inside the vehicle from radiation damage.
Choose Chalco as the supplier for the armor plate project
Chalco hot rolling project utilizes the German Sigma (1+4) 4500mm continuous rolling line, and the cold rolling project uses the German Sigma six-high cold rolling mill. With a maximum width of 2650mm and thickness up to 500mm, our aluminum plates undergo stress relief to prevent deformation during cutting. We are among the few capable of producing ultra-wide and ultra-thick aluminum plates.
Chalco has developed reliable and repeatable cold forming processes in the field of armor plate production, avoiding common faults such as cracks, and has received scientific and engineering validation support. Chalco has also developed innovative material testing methods to verify and ensure the optimal material elasticity of its aluminum armor plate products.
Chalco's high-quality armor plate has complete quality certification, complete products, large inventory, short delivery time, and discounted prices. Welcome to inquire and support price comparison.
Chalco armor plate product quality inspection
Unlike other functional aluminum plates, armor plates have higher and stricter quality requirements due to the unique nature of their use areas. Chemical composition, strength, hardness, processability, and corrosion resistance must be strictly controlled during and after production.
Chalco product development and production are within the MIL-DTL standard range, and can provide finished product testing to ensure quality meets customer requirements.
Initial product inspection testing methods
- Chemical composition: extract samples for chemical analysis from each plate selected for ballistic testing.
- Mechanical performance: extract tensile test samples from each board selected for ballistic testing.
- Ballistic testing: according to the standards in the standard attachment, two 12x36 inch plates of each thickness provided in the contract are taken for ballistic testing.
- Stress corrosion test: the stress corrosion test samples are extracted from the same plate selected for ballistic testing.
Product compliance inspection testing methods
- Chemical composition: when tested according to the provisions of this standard, the sample must meet the chemical composition requirements.
- Mechanical properties: for tensile testing, samples are randomly selected from different plates in the batch, and only one tensile test sample is taken from each sample.
- Ballistic testing: randomly select a 12x36 inch plate from each batch for ballistic testing.
- Stress corrosion test: randomly select a 12x12 inch plate from each batch for this test.