Anodized Sheets for Lighting, Sign and Cookware
Anodizing creates a durable, corrosion-resistant film on aluminum plates, ideal for products like lamps and road signs.
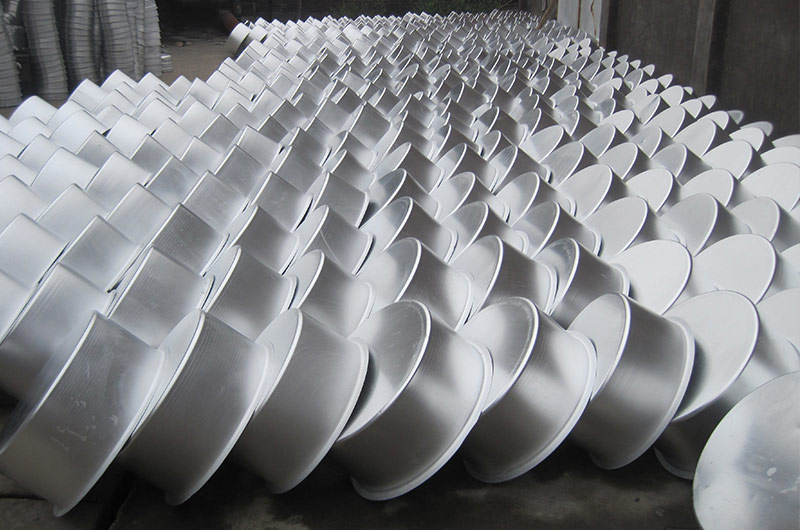
Specifications for anodized aluminum sheet and strip for lamps, signs and kitchen utensils
Craftsmanship: Cold rolling (CC), hot rolling (DC)
Standard: EN 14392,ASTM B632,B209,AMS-QQ-A-250/2,Mil-A-8625,AAMA 611-11,EN485-2,ISO 9000,GB/T3880-2012
Package: Standard export wooden pallet, wrapped in kraft paper, each package has moisture-proof agent. Standard packaging is about 1 ton/pallet. Pallet weight can also be based on customer's requirements.
Note: The materials listed above are available in various sizes and shapes (discs, aluminum coils, aluminum plates) according to customer requirements.
All products come with peelable self-adhesive polyethylene protective tape to prevent scratches.
Applications of anodized aluminum plate strips for lamps, signs and kitchen utensils
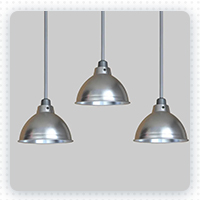
Anodized aluminum plate for lighting
Anodized aluminum plate for lighting provides a dust-proof enclosure for enhanced lighting and also ensures even distribution of light, providing even illumination to all corners for a more perfect lighting effect.
- Alloy 1050,1060,3003,6063,8A06
- Temper O, H14, H16, H18
- Film thickness 2.5-30μm (or according to customer requirements)
- color Oxidized true color (silver), black, purple, red, blue, gray, copper, green
- Thickness 0.1-2.5 mm
- Hot selling width 50-1520 mm
- Reflectivity 78%-96%
- Diffuse reflectance ≤12%
Advantage of anodized aluminum plate for lighting
- High reflectivity, up to 90%.
- Good heat dissipation.
- Resistant to corrosion, fingerprints, and does not absorb dust.
- Light weight, high plasticity, easy for further processing.
- The surface has high hardness and is scratch-resistant.
- Environmentally friendly and recyclable.
- Good surface performance, guaranteed to be free of obvious scratches, oil stains, oxidation, and black spots
Application of Anodized aluminum plate for lighting
Outdoor lighting, grille light panels, LED lighting, tri-proof lamps, car headlights, DIY lamps, spinning lampshades
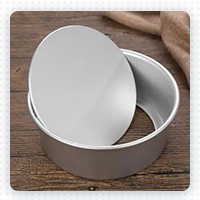
Anodized aluminum plate for cookware
Statistics show that about half of the world's cookware is made of aluminum because aluminum cookware can significantly improve corrosion resistance, thermal conductivity and heat resistance. Hard-anodized aluminum cookware ensures that it will not react with or penetrate food, ensuring food safety.
- Alloy 1050,3003,5052,6061
- Temper O, H14, H18, H22, H24
- Film thickness 2.5-200μm (or according to customer requirements)
- Thickness 0.3-10.0 mm
- Hot selling thickness 0.3-6.0 mm
- Hot selling width 500-1600 mm
- Thermal conductivity 2.367W/(CM·K)
- color Silver, black, metallic gray, metallic gray, gold, red
Advantage of anodized aluminum plate for cookware
- High plasticity and good processing performance.
- The grain size and elongation are well controlled, making it suitable for deep drawing and spinning.
- The hard anodized layer will not crack or peel off.
- Wear-resistant and corrosion-resistant.
- Available in various colors.
- Good thermal conductivity.
- Food grade anodized to EN 14392 standard.
- Environmentally friendly materials, green and non-toxic.
- The surface performance is good, ensuring no obvious scratches, oil stains, oxidation, or black spots.
- The price is cheaper than other metals.
Application of anodized aluminum plate for cookware
Aluminum woks, pans, non-stick pans, pressure cookers, aluminum trays, aluminum bakeware, kettles, plates, bowls, kettles
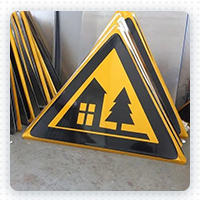
Anodized aluminum plate for traffic signs
Due to its lightweight, wear resistance, weather resistance, and high hardness, aluminum plates are commonly used for making traffic signs. The metal surface of aluminum retains a high reflectivity after anodizing. Over the years, the most popular material for traffic signs has been 5052-H38, valued for its high strength, weather resistance, and corrosion resistance, particularly important in coastal and cold climates.
- Alloy 3003,3004,5052,6061
- Temper H14,H18,H22,H38,T6
- Film thickness 2.5-200μm (or according to customer requirements)
- color Blue, white, red, yellow, orange, black, natural metallic color
- Thickness 0.2-10.0 mm
- Width 50-1650 mm
Advantage of anodized aluminum plate for traffic signs
- High hardness, scratch-resistant, wear-resistant, non-magnetic
- Higher grain grade and good surface finish.
- preservative
- High reflectivity, good reflective effect
- Light weight, easy to process and cut
- The oxide layer will not crack or peel off
- A variety of colors to choose from, bright colors and not easy to fade
- Environmentally friendly and recyclable
Application of anodized aluminum plate for traffic signs
Traffic signs, scenic park signs, commercial street guides, hospital campus school signs, publicity boards, bus stop signs, floor signs, warning signs, reminder signs
Frequently Asked Questions about Anodized Aluminum Strips for Lamps, Signs, and Kitchenware
Which Temper should you choose for anodized aluminum strips for lamps, signs, and kitchenware?
When customers purchase anodized aluminum sheets for producing various kitchenware, lamps, and sign products, different thicknesses and widths are required. For example, pot lids may require H12 or H14 states, while aluminum kettles may need the O state.
For customers using the O-state aluminum sheet for making thick kitchenware and lamps, we recommend adopting the H14 state. This allows customers to achieve the same hardness with a thinner aluminum sheet, thereby saving costs.
How to cut aluminum discs from aluminum plate rolls?
Stamping machine (rounding machine): The aluminum sheet coil cutting production line is a fully automatic integrated production equipment for aluminum discs. It can directly punch and drop aluminum discs on the aluminum sheet coil, eliminating the need for cutting and slitting processes.
This significantly improves the company's production efficiency and material utilization, shortening the delivery cycle. The amount of waste is fundamentally reduced, and the raw material utilization rate reaches 80% or more. Stamping can be done for diameters ranging from 100mm to 1200mm.
Circular cutting machine (shearing machine): It is a very simple production equipment that uses two disc-shaped scissors for cutting based on the different positions of the two scissor shafts and the different angles with the sheet.
In production, we need to first cut the aluminum sheet into square pieces. Then, the aluminum sheet is slowly stretched into a circular shape using a circular shear.
The production speed of the circular cutting machine is relatively slow, and the edges are prone to burrs. Therefore, it is not suitable for large-scale production. Circular shearing machines are generally used for producing aluminum circles with a diameter above 800mm.
What is the difference between cold-rolled (CC) aluminum coils and hot-rolled (DC) aluminum coils?
Cold-rolled aluminum coil is produced by passing an aluminum coil through a cold rolling mill, while hot-rolled aluminum coil is formed through high-temperature heating and rolling.
CC (Continuous Casting) aluminum coil is mainly used for spinning processes. DC (Direct Casting) aluminum coil is suitable for stamping and deep drawing production processes.
Hot-rolled aluminum coil has good surface quality, excellent mechanical properties, good ductility, and effective resistance to oxidation.
Anodized aluminum sheet for lamps, signs, and kitchen utensils with hem and tear defects
The cracking of anodized aluminum sheets during bending is a common occurrence. Even with extremely thin sheets, there may be hairline cracks. The thicker the anodized aluminum sheet, the more severe the cracking during bending.
To address this issue, three key aspects should be considered:
High-Quality Raw Materials: Ensure the use of high-quality raw materials by selecting suitable alloys and specifications. This helps improve the processability and bending performance of the aluminum sheet.
Adjustment of Coating or Anodizing Parameters: Consider whether adjustments to the coating or anodizing process parameters are needed to enhance the surface properties of the aluminum sheet and reduce the likelihood of tearing.
Process Improvement: Review the entire production process to identify potential factors contributing to bending-related tearing. Implement necessary improvements to the production process.
Addressing these aspects can contribute to minimizing or preventing cracking issues during the bending of anodized aluminum sheets.
Our employees, on average, have nearly ten years of work experience at Chalco, enabling us to provide valuable insights into many of your substantive questions.
Please feel free to contact us immediately to learn more about how we can assist you.
Chalco aluminum plate processing capabilities
Chalco employs a cast-rolling continuous rolling process to develop deep-drawn anodized aluminum sheet strips.
This method eliminates the need for hot rolling processes and offers advantages such as energy savings, reduced emissions, faster production, shorter cycles, high-quality output, and lower costs.
We also focus on controlling the grain size and elongation of aluminum coils. The elongation of the produced aluminum sheet coils reaches 30% to 35%. The grain size is at the first level, with a smooth and scratch-free surface, clean and free of oil stains, and smooth edges without burrs.
It complies with RoHS, meeting environmental standards, making it the preferred choice for excellent automotive lamp components, spun kitchenware, and traffic signs.
During the anodizing process, we strictly control key parameters such as temperature, current density, and electrolyte composition to ensure that the structure and properties of the anodized film meet the standards.
Finally, the factory has hired experienced technical personnel with rich production experience, actively summarizing the experiences of previous end customers.
We rigorously control the production process, strive for excellence in product quality, and effectively avoid issues such as orange peel, square edges, lotus leaf edges, and burrs caused by production reasons.